Chemical Laboratories
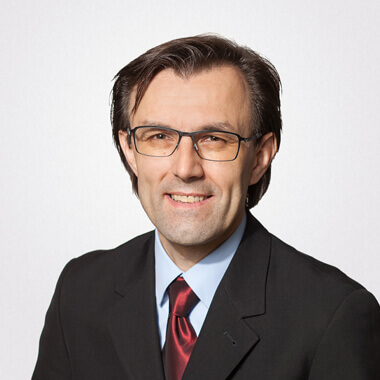
Head: Chemical Laboratories
Our state-of-the-art chemical laboratories provide production with critical information for process control, product certification, and environmental monitoring. To determine the composition of metallic and non-metallic substances such as steel, non-ferrous alloys, input materials and by-products of stainless steel production, we use inorganic chemical analysis methods.
Process Analytics and Solids Analysis
Tasks: Analysis of solid samples with the aim of short response times with the highest precision and correctness at the same time.
Methods: X-ray and spark spectrometry as well as combustion analysis and melt extraction.
Wet Chemistry
Tasks: Trace analysis for process samples as well as determination of the main and minor components of difficult matrices, supply of solids analysis with certified calibration samples and reference materials, special raw material and waste analyses, analysis of environmentally relevant samples.Methods: Classical wet chemical analysis methods in combination with state-of-the-art optical spectrometry, mass spectrometry and chromatography.
Corrosion Testing
Tasks: Corrosion investigation of steels and alloys.
Absorption cooling, heat recovery heating and ventilation
Methods: Various methods in accordance with international standards and specific regulations for testing resistance to generally ablative corrosion, intercrystalline corrosion, stress corrosion cracking, pitting corrosion – including electrochemical test methods.
The heating energy supply of the new chemical laboratory will be ensured by decoupled industrial waste heat in the plant and at the same time the heating power requirement for the ambient air of the laboratory processes will be significantly reduced by a closed-loop system from the laboratory exhaust air.
In addition, cooling will be provided by an absorption refrigeration system with a cooling capacity of around 850 kW and cooling towers on the roof. Existing process waste heat potential from the plant will also be utilised as expulsion energy.
‘This project is co-financed by the European Regional Development Fund’
Testing Laboratories
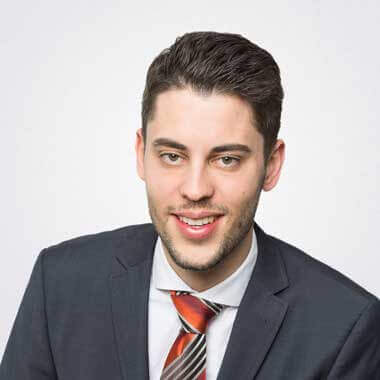
Head: Mechanical Laboratory
Mechanical-Technological Testing Laboratories and Materials Testing
Tasks: Determination of mechanical parameters.
Methods: Execution of tensile, hot tensile, notched impact and creep tests as well as hardness tests according to Brinell, Rockwell and Vickers on steel and non-ferrous alloys in accordance with international standards and regulations.
Metallography
Tasks: Determination of microstructure parameters on samples and components – including sample preparation, etching and photo documentation – according to test standards and customer specifications.
Methods: Determination of structure, grain size and degree of purity, decarburization, etc.
Heat treatment
Tasks: Heat treatment of samples and components according to the requirements of our customers.
Methods: Heating in system-monitored laboratory furnaces with air atmosphere and in vacuum, supplemented by salt baths and deep-freeze treatments for residual austenite conversion. Water and oil are available as quenching media.
Metallurgical & Physical Laboratory
Tasks: Execution of hot forming simulations, differential thermal analyses and dilatometric investigations, heat treatment and forming simulation, creation of ZTU and ZTA diagrams, deep-freeze simulations, determination of linear expansion coefficients and investigation of recrystallization and precipitation processes.
Methods: Material and failure analyses of microstructure samples and fractures as well as qualitative analysis of non-metallic inclusions with scanning electron microscopes, measurement of physical properties of materials such as testing of soft magnetic materials, strain and stress analyses using strain gauge technology as well as X-ray diffraction analyses (residual austenite, phase analysis).
Certifications
In the following sections you will find all certificates that are valid for the production site Kapfenberg – voestalpine BÖHLER Edelstahl GmbH & Co KG
NADCAP – Location Kapfenberg
NADCAP – Location Kapfenberg
Contacts
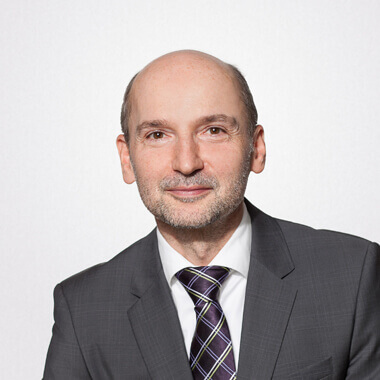
Head: Testing and certificates